Principle and applications:
Two extruders group can reach a high achievement from its advantages. twin screw extruder has an outstanding performances in material conveying, high effective plasticizing and compounding, shearing and dispersing, and free back pressure reflux happening. Single screw extruder has an outstanding performances in extruding ability under high pressure, low speed rotation, low shearing, overheating limit in production.
Higher productivity and yield, widely used in heat sensitive material and mass degassing operation. Such as: PVC, XLPE, free halogen flame-retardant cable, shielding material, high concentration carbon black masterbatch, pro-treatment of rubber dewatering,etc.
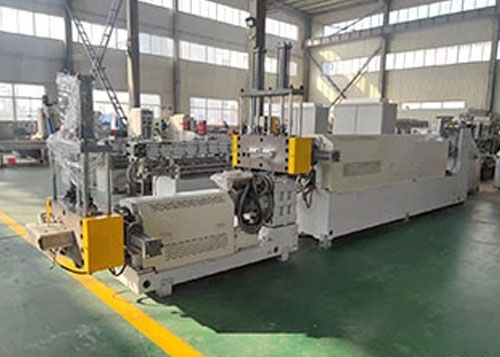
Technical parameter of the extruder group:
1. The first stage screw extruder
1.L/D:28 :1
2.Screw diameter:85~180
3.Motor power:55~300KW
4.Speed:10~150rpm
5.Cooling method:forces wind cooling
6.Lubrication:forces lubricating
7.Heating method:electric heater
8.Control zone: 7 zones
9.Control zone for head: 2 zones
10. Vacuum degas: an enlarged one
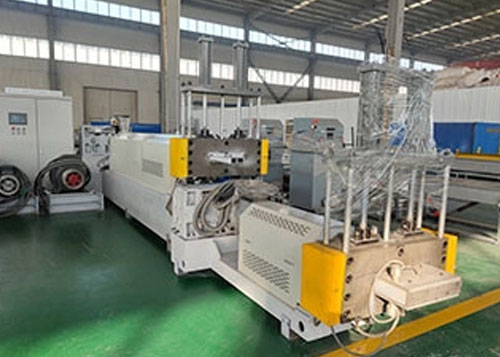
The Second stage screw extruder
1.L/D:10 :1
2.Screw diameter:150~200
3.Motor power:55~90KW
4.Speed:10~120rpm
5.Cooling method:forces wind cooling
6.Lubrication:forces lubricating
7.Heating method:electric heater
8.Control zone: 4 zones
9. Pelletizing method: Water-ring pelletizing system
Layout: Frist Stage extruder is high speed co-rotating twin screw extruder, second stage extruder is low speed single screw extruder. Both extruder are placed vertically in production area.
Screw Kneading block built on modular principle allows various L/D ratio of screw easily be changed to suit different material. Screw component made of high speed & wear-resisting steel.
Barrel
By means of the replaceable screw barrel sections, the processing sections is devided into individual zones. The barrels are heated electrically. In addition, the barrels are provided with longitudinal bores for cooling with water. Uniform temperature distribution, namely on the circumference of the eightshaped barrel bore, is achieved by a reverse forceflow temperature
control circuit. Connections of pipes for temperature control are
in groove-tongue design to balance alternating thermal stress and avoid leakage.
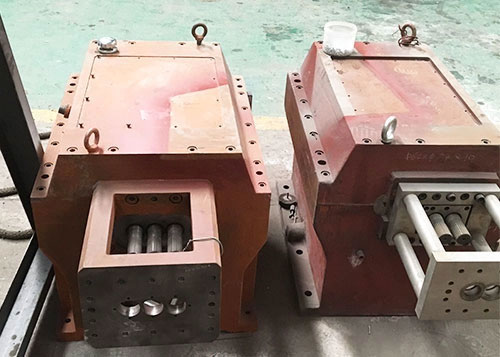
High torque Transmission Gear Box Twin Screw Extruder Triple screw Extruder