Triple Screw Plastic Extruder Can be used for reaction extrusion, Color masterbatch, filler masterbatches making, Engieering polymer compounding machine
Detailed Product Description
Condition: | New | Plastic Processed: | PP PE PVC ABS |
Screw Design: | triple-screw | Automatic Grade: | Working Automatically |
Voltage: | 380V | Power(W): | 75/90/132 Kw |
Dimension(L*W*H): | 4.2m*1.5m*2.4m | Weight: | 3000kg |
Certification: | CE ISO9001 | After-sales Service Provided: | Engineers Available To Service Machinery Overseas |
Item: | Triple Scew Plastic Extruder | Raw Material: | PP/PVC/PE/ABS |
Usage: | Produce Color/fillier Masterbatch And Other Plastic Products | Color: | Customizable |
Automatic Grade: | High Antomatic | Screen Changer: | Hydrulic Screw Changer |
Diamater Of Screw: | 52/65/75 mm | L/D: | 36:1-56:1 |
Speed: | 400/500/600rpm |
filler masterbatches making machine with three Screw Plastic Extruder
1.Electric control system of Three screw extruder
2.The Gearbox
3.Mixing and Feeding system
4.The compounding system
5. pelletizing system
Main Features
Three screw construction with parallel diamater in same direction.
High shear efficiency and good plasticizing effect.
Good practice and dispersal effect.
High output and low energy consumption.
Good exhaust performance.
Technical Date of twin screw extruder: | ||||
Model | Screw dia
(mm) |
Screw speed rpm | L/D | Main motor powder(kw) |
SJSH-52 | 52 | 400/500/600 | 20:1-64:1 | 75-90 |
SJSH-65 | 65 | 400/500/600 | 20:1-64:1 | 90-132 |
SJSH-75 | 75 | 400/500/600 | 20:1-64:1 | 132-250 |
Detailed Images
1. Name: three Screw
The screw elements material is W6Mo5Cr4V2
The core axis is made of high quality alloy steel 40CrNiMo
2.Name: Gearbox
Parallel tri-axial structure is combination of reduction and matrix. The gear is made of high quality alloy (20CrNi2Mo).Drive bearing:
Lubrication: Gear bearings in the gear box will be of oil immersed. There is hydraulic lubrication in the gear engagement and gear bearings.
Cooling: Lubricated cooling adopts shell and tube cooler and circulated water cooling method.
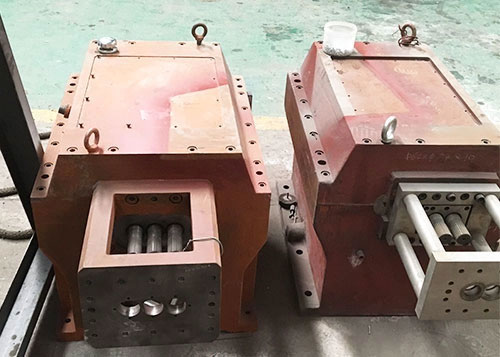
High torque Transmission Gear Box Twin Screw Extruder Triple screw Extruder
3.Name: Barrel
Diameter:62.4mm
Standard: L/D: 40:1, and other available
Length: 10 sections for 40:1, 10*240mm=2400mm
Material: made of 45# forged steel with the abrasion-resistant alloy 101(Ni-Fe-Cr-W) inside, which is smooth and abrasion resistant. The hardness is HRC60-64
Pelletizing Applications:
1. Water cooling strand pelletzing
- Glass-filled reinforcement: PP,PA,PC,ABS,PET +up to 50% glass fibre reinforcing
- Incorporation of fillers: PP,PE, +up to 80% Calcium Carbonate / Talc
- Color masterbatch: all kinds of color mater batch
- PET scraps recycling
- All kinds of cable compounding
- Degassing extrusion
- Special mater batch
- High quality polymer alloy: PC+ABS, PA+ABS, PP+ABS
2. Air cooling pelletizing
- Air cooling hot face pelletizing systems can be applied for processing of some polymers, including: PVC, LLDPE, MB, high filled Calcium Carbonate MB, degradable MB, LSFH, Carbon Black MB, Cross-link PE, etc. Air cooling hot face pelletizing systems can avoid the moisture involved during pelletization process with replacing of air cooling. the main components usually include extrusion die plates, pelletizer, cyclone cooler and conveying units, shifter, silo and package units.
3. Water ring pelletizing
- Water ring hot face die pelletizing system can be applied to some polymers, including: PP,PE, PS, TPU, EVA,etc. The main components include plate, pelletizer, water circulating dewater, silo and package system.
4. Under water pelletizing
- Elastomer TPU, TPE, TPO, POE,EVA, SBS
- Thermo plastic PE, PP, PS, PA, modified.
- Low viscosity reaction polymer, all kinds of hot melt adhesive,
- Pure polymer, capacity over 500kg/h
Application
1. High dispersibility, high filling capacity, such as modification of polyolefin, modification of engineering plastics,etc.
2. Mixing, venting and devolatilization, and homogeneous residence time for high reactive extrusion, such as XLPE cable,silance crosslinking cable, TPE,etc.
3. High concentration of masterbatch and other functional masterbatches with high dispersing effect, such as high concentration black,white materbatch, highly filled flame retardant, semiconductive material,etc.
4. In-line compounding molding of film, board and injection parts, such as breathable film, long glass fiber reinforced plastic structrural parts.
Our Service
Pre-sales service
full introduction for product characteristic and application.
Provide the economical and effective equipment configuration and solution.
Provide useful information including: the equipment working status and conditions
Provide test or trial experience.
Middle-sales service
Design and layout for the working space and pipes, public project condition.
Constantly follow up the project progress.
Work together with you in the product processing situation, screw configuration, production arrangement,etc.
After sales service
Provide on-site installation, commission, training lesson.
Record the user detailed document.
Stock for spare parts, don’t worry about the repair while new machine operation instead of old machine.
Instantly provide the user application for new product processing.
regularly follow up the equipment and feedback.
one year warranty